Cromolly front axles can break.
#21
#22
JK Super Freak
Join Date: May 2008
Location: Grand Junction, CO
Posts: 1,279
Likes: 0
Received 0 Likes
on
0 Posts

Well I think there is a flaw in the computation. You just have the torque at the out of the engine with all gear chained up. In fact you have to divide by 2 (output of the T.case) and if you were lock (axle) divide by 2 again (50% on each wheel) so the result might be: 2'925.5 ft/lb on this axle shaft.
#24
JK Super Freak
Join Date: Oct 2006
Location: Montclair, VA
Posts: 1,142
Likes: 0
Received 0 Likes
on
0 Posts

sorry to hear about the break, but awesome it's getting replaced! i guess I need to invest in some soon too... man my list keeps getting longer and longer....
#25
JK Jedi Master

Well I think there is a flaw in the computation. You just have the torque at the out of the engine with all gear chained up. In fact you have to divide by 2 (output of the T.case) and if you were lock (axle) divide by 2 again (50% on each wheel) so the result might be: 2'925.5 ft/lb on this axle shaft.
Your theory may sound good to you but it is wrong. I've talked to nobody who said a D44 axle would give at anywhere near 2925; 7000 is the floor for a stock D44 shaft. The other three wheels could turn quite freely; and did after the rear axle broke. When you are all locked up and nothing is turning the one that is in the bind is providing all the resistance. You could do the same thing with the Jeep jacked up in the air with three wheels able to turn freely but only one restrained; say chained up to a giant torque gauge that could read torque (easy to do, we do it at work). None of the other wheels will turn and all the torque output will be read on the torque gauge. Until the point the axle breaks and then the torque will be deliverd to the other wheels.
It may have been more like this:
All 4 tires in the mud, with one being harder to turn than the others, added up to more resistance than the engine could turn.
The weak link broke, and suddenly all the torque was going to only 3 tires, which provided significantly less resistance. Therefore, the engine could spin them.
It's too hard to say at what torque the shaft failed.
Was the locker the OEM Tru-Loc? If so, I would say it was stronger than most people give it credit for.
#26
JK Super Freak

For the long (inner)shaft you want flex. So the nipple look is the right indicator ( your friend would be correct with that). For the outer shaft, you don't won't get that flex as the shaft is not long enough to provide that kind of give. A nipple on the outer shaft is an indication that the metal is too elastic for that application. That elasticity would apply stress to the splines.... not a desired trait. You inner shaft should act as the spring.
#28
JK Junkie
Thread Starter

We found this when we went to replace the stub shaft.
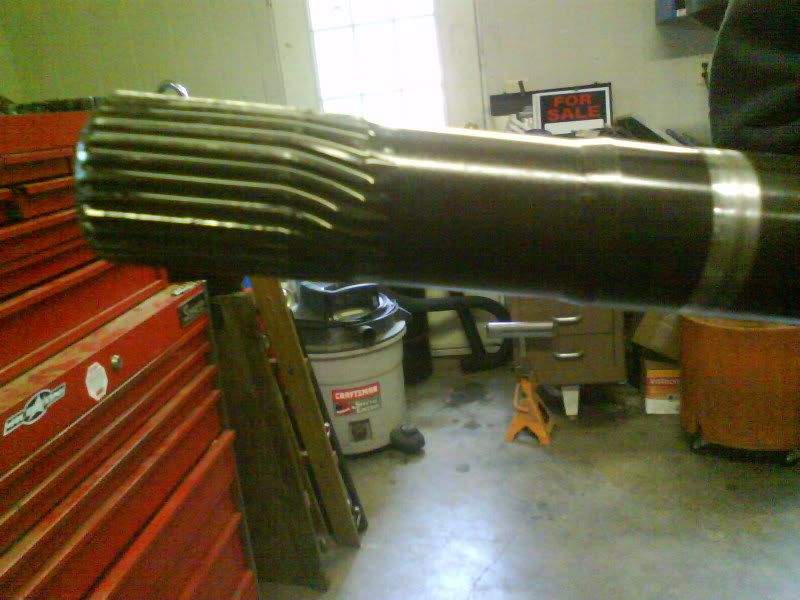
Many thanks to Dave and his Dad @ Northridge for doing all the hard work and the warranty stuff.
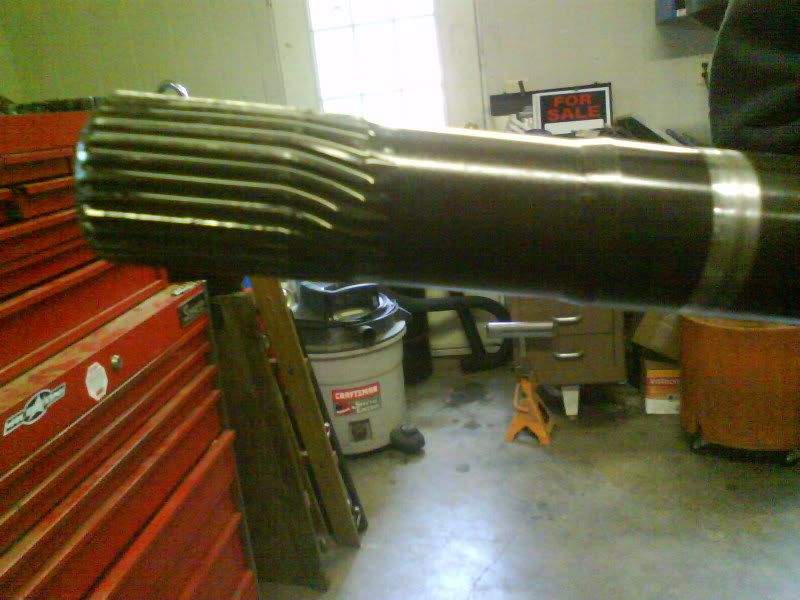
Many thanks to Dave and his Dad @ Northridge for doing all the hard work and the warranty stuff.
#29
JK Super Freak
Join Date: May 2008
Location: Grand Junction, CO
Posts: 1,279
Likes: 0
Received 0 Likes
on
0 Posts

Barney Bros, my local 4x4 shop that did my gears, told me yesterday that they've had to replace several Rubi lockers after axles broke.
I had to pull my front carrier out to remove the stub and everything looked good. I seem to be developing a noise in my rear axle. A stethoscope indicates that it's probably the pinion bearing going south. Barney Bros is going to pull it apart next week to replace the bearing and while out they're going to check out the elocker for me.
From what I can gather it seems that taking out the Rubi locker seems more common with stock shafts than with CM shafts. I have no idea why or how this could be. Could it be that the stockers are cut splines and the CM shafts are rolled splines?
All I know is that I'm going to take it a little easy until the container with ARB lockers for the Rubi axles arrives. I won't mind replacing the locker with an ARB; but it would really frost my ass to have to buy a factory unit.
#30
JK Super Freak

Sorry, I get all geeky when talking about engineering. Can't help myself... did it for a living.