Anyone Make Aluminum Skid Plates
#42
JK Super Freak
Join Date: Sep 2006
Location: Wiliamsburg, VA
Posts: 1,266
Likes: 0
Received 0 Likes
on
0 Posts

How about teflon skids? Nothing sticks to teflon. Or how about kevlar? If it stops a bullet, it will stop a rock. Or gore-tex for water proofing the underbelly?
#43
JK Super Freak
Join Date: May 2008
Location: Grand Junction, CO
Posts: 1,279
Likes: 0
Received 0 Likes
on
0 Posts

Seeing as how my Jeep is a daily driver, I have no desire to ever take it on a trail that harsh. The vehicle is designed for a certain amount of weight. With the amount of skid plates, bumpers, giant wheels and tires, etc, that a lot of people add, it starts to stress the factory components that they dont replace, like the brakes, tranny, etc.
If the stresses cause something to break make it stronger! Put a HD tranny cooler on to help the tranny run cool; remember about everything we do aftermarket is exceeding the factory design envelope.
#44

Before you get all workd up about aluminum skid plates find a nice big plate of aluminum and then grab a nice big sharp edged rock and drag it across the aluminum. Stuff that slides on steel digs into aluminum and becomes difficult to slide. I have an 3/16 aluminum liner on the inside of my tailgate; it is a bitch to load anything as everything seems to drag and stick. My old PU had 1/8 of steel on the tailgate and worked out great.
I'd worry less about the wt of steel skids as the wt is down low. Now wt up high like the Range Rover (and seemingly FJCruiser) guys are doing on roof racks worries the dickens out of me.
I'd worry less about the wt of steel skids as the wt is down low. Now wt up high like the Range Rover (and seemingly FJCruiser) guys are doing on roof racks worries the dickens out of me.
If you notice the length of the gouges, scratches and scrapes, they don't stop because the rocks dug in, I either picked another line or kept going as you can tell by the length of many of them.
Don't for a second believe all the myths and misconceptions about using aluminum in the right alloy for skids.

#45

Well, how about if I take that same sheet of aluminum, grab a big sharp rock and then set about 2000 lbs on it, or about half the weight of the rig? Would that work for you? I hope so, I've been doing exactly that for the last 6 or 7 years with the same sheet of aluminum for a flat belly skid on my TJ.
If you notice the length of the gouges, scratches and scrapes, they don't stop because the rocks dug in, I either picked another line or kept going as you can tell by the length of many of them.
Don't for a second believe all the myths and misconceptions about using aluminum in the right alloy for skids.
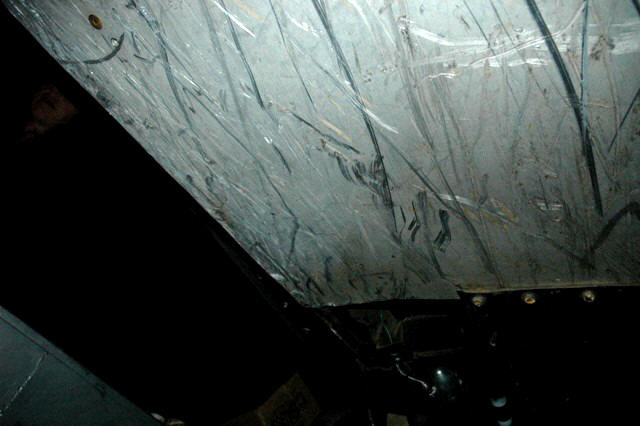
If you notice the length of the gouges, scratches and scrapes, they don't stop because the rocks dug in, I either picked another line or kept going as you can tell by the length of many of them.
Don't for a second believe all the myths and misconceptions about using aluminum in the right alloy for skids.

Blaine good seeing you over on the JK side.
#47

Howdy. I'm a bit surprised reading all the responses to the use of the correct aluminum for armor. I'm guessing that unlike you, most of the JK owners are newish to offroading in that this is likely their first serious offroad vehicle.
Apparently all the stuff we've been doing over the years with aluminum on the non JK boards has finally rubbed off on most and there's not nearly the resistance to strong lighter weight armor on them as there is here.
A bit of education always goes a long way I guess, in time the rest will catch up as well.
I think the biggest problem is most don't know that just like steel and all of it's various alloys for different uses, aluminum probably has just as many or more for the same reasons.
Another thing that gives Aluminum a bad rap is manufacturers attempt to use it straight across as a swap and don't take enough care in their alloy selection and engineering.
Similar to an offroad desert racer using HREW tubing to build his chassis from, it won't last long and the next one will be made from Quality DOM or 4130N chrome molly tubing. They're both steel, but they are nowhere near the same animal.
So, fab shops building stuff for Jeeps substitute 5052 which is great because you can bend and form it just like HRPO steel, but at a great sacrifice in strength. The vastly stronger 6061 T6 is much harder to work with if you don't have experience, so it's often overlooked or just ignored.
On the TJ, we've had beyond phenomenal success with aluminum full corners in the same thickness as steel sides. As of yet, we've not managed to dent one and we've tried whereas my steel corners and sides have dents all over them from the same trails. The cool thing is a full set of aluminum sides is about 35 lbs (42 until you cut the wheel openings) vs 100+ lbs (140 until you cut the openings) for steel. I did some comp cut corners for a TJ I built and you could reach down and pick them of the ground with two fingers pinching them from the top very easily.
Apparently all the stuff we've been doing over the years with aluminum on the non JK boards has finally rubbed off on most and there's not nearly the resistance to strong lighter weight armor on them as there is here.
A bit of education always goes a long way I guess, in time the rest will catch up as well.
I think the biggest problem is most don't know that just like steel and all of it's various alloys for different uses, aluminum probably has just as many or more for the same reasons.
Another thing that gives Aluminum a bad rap is manufacturers attempt to use it straight across as a swap and don't take enough care in their alloy selection and engineering.
Similar to an offroad desert racer using HREW tubing to build his chassis from, it won't last long and the next one will be made from Quality DOM or 4130N chrome molly tubing. They're both steel, but they are nowhere near the same animal.
So, fab shops building stuff for Jeeps substitute 5052 which is great because you can bend and form it just like HRPO steel, but at a great sacrifice in strength. The vastly stronger 6061 T6 is much harder to work with if you don't have experience, so it's often overlooked or just ignored.
On the TJ, we've had beyond phenomenal success with aluminum full corners in the same thickness as steel sides. As of yet, we've not managed to dent one and we've tried whereas my steel corners and sides have dents all over them from the same trails. The cool thing is a full set of aluminum sides is about 35 lbs (42 until you cut the wheel openings) vs 100+ lbs (140 until you cut the openings) for steel. I did some comp cut corners for a TJ I built and you could reach down and pick them of the ground with two fingers pinching them from the top very easily.
#48

Howdy. I'm a bit surprised reading all the responses to the use of the correct aluminum for armor. I'm guessing that unlike you, most of the JK owners are newish to offroading in that this is likely their first serious offroad vehicle.
Apparently all the stuff we've been doing over the years with aluminum on the non JK boards has finally rubbed off on most and there's not nearly the resistance to strong lighter weight armor on them as there is here.
A bit of education always goes a long way I guess, in time the rest will catch up as well.
I think the biggest problem is most don't know that just like steel and all of it's various alloys for different uses, aluminum probably has just as many or more for the same reasons.
Another thing that gives Aluminum a bad rap is manufacturers attempt to use it straight across as a swap and don't take enough care in their alloy selection and engineering.
Similar to an offroad desert racer using HREW tubing to build his chassis from, it won't last long and the next one will be made from Quality DOM or 4130N chrome molly tubing. They're both steel, but they are nowhere near the same animal.
So, fab shops building stuff for Jeeps substitute 5052 which is great because you can bend and form it just like HRPO steel, but at a great sacrifice in strength. The vastly stronger 6061 T6 is much harder to work with if you don't have experience, so it's often overlooked or just ignored.
On the TJ, we've had beyond phenomenal success with aluminum full corners in the same thickness as steel sides. As of yet, we've not managed to dent one and we've tried whereas my steel corners and sides have dents all over them from the same trails. The cool thing is a full set of aluminum sides is about 35 lbs (42 until you cut the wheel openings) vs 100+ lbs (140 until you cut the openings) for steel. I did some comp cut corners for a TJ I built and you could reach down and pick them of the ground with two fingers pinching them from the top very easily.
Apparently all the stuff we've been doing over the years with aluminum on the non JK boards has finally rubbed off on most and there's not nearly the resistance to strong lighter weight armor on them as there is here.
A bit of education always goes a long way I guess, in time the rest will catch up as well.
I think the biggest problem is most don't know that just like steel and all of it's various alloys for different uses, aluminum probably has just as many or more for the same reasons.
Another thing that gives Aluminum a bad rap is manufacturers attempt to use it straight across as a swap and don't take enough care in their alloy selection and engineering.
Similar to an offroad desert racer using HREW tubing to build his chassis from, it won't last long and the next one will be made from Quality DOM or 4130N chrome molly tubing. They're both steel, but they are nowhere near the same animal.
So, fab shops building stuff for Jeeps substitute 5052 which is great because you can bend and form it just like HRPO steel, but at a great sacrifice in strength. The vastly stronger 6061 T6 is much harder to work with if you don't have experience, so it's often overlooked or just ignored.
On the TJ, we've had beyond phenomenal success with aluminum full corners in the same thickness as steel sides. As of yet, we've not managed to dent one and we've tried whereas my steel corners and sides have dents all over them from the same trails. The cool thing is a full set of aluminum sides is about 35 lbs (42 until you cut the wheel openings) vs 100+ lbs (140 until you cut the openings) for steel. I did some comp cut corners for a TJ I built and you could reach down and pick them of the ground with two fingers pinching them from the top very easily.

#49

I know several off road racers in both SNORE and SCORE. They desert racers are much more abusive to the skid plates than rock crawlers. When was the last time a rock crawler hit a their skid at 100+ mph. Aluminum has been the metal of choice for many, many years for desert racing. I also know some competitive rock crawlers in Utah. Who have used steel, switched to aluminum then the plastic. All have the same complaints. Steel is to heavy, aluminum and plastic stick to the rocks.
They are now switching to titanium. It is a little heaver then aluminum but slides off of the rocks. I have seen where the skid plate has hit hard enough to bend the support structure and only left a scratch on the plate. The driver felt the hit but it never slowed the car down.
As with most metals the alloy makes a significant difference. ASTM grade 5 also known as 6/4 seems to work well, others might work better but stay away from the lower ASTM grades.
They are now switching to titanium. It is a little heaver then aluminum but slides off of the rocks. I have seen where the skid plate has hit hard enough to bend the support structure and only left a scratch on the plate. The driver felt the hit but it never slowed the car down.
As with most metals the alloy makes a significant difference. ASTM grade 5 also known as 6/4 seems to work well, others might work better but stay away from the lower ASTM grades.
#50

I know several off road racers in both SNORE and SCORE. They desert racers are much more abusive to the skid plates than rock crawlers. When was the last time a rock crawler hit a their skid at 100+ mph. Aluminum has been the metal of choice for many, many years for desert racing. I also know some competitive rock crawlers in Utah. Who have used steel, switched to aluminum then the plastic. All have the same complaints. Steel is to heavy, aluminum and plastic stick to the rocks.
They are now switching to titanium. It is a little heaver then aluminum but slides off of the rocks. I have seen where the skid plate has hit hard enough to bend the support structure and only left a scratch on the plate. The driver felt the hit but it never slowed the car down.
As with most metals the alloy makes a significant difference. ASTM grade 5 also known as 6/4 seems to work well, others might work better but stay away from the lower ASTM grades.
They are now switching to titanium. It is a little heaver then aluminum but slides off of the rocks. I have seen where the skid plate has hit hard enough to bend the support structure and only left a scratch on the plate. The driver felt the hit but it never slowed the car down.
As with most metals the alloy makes a significant difference. ASTM grade 5 also known as 6/4 seems to work well, others might work better but stay away from the lower ASTM grades.