On Board Hot Water
#1

We have a 2012 JKU Rubi that we like to camp out of and it’s nice to have hot water for cleaning up after a day out and about. I’ve tried propane fired water heaters but didn’t like how flimsy they were, how they worked, and how much space they took up, so I decided to install an on board heat exchanger using engine coolant. I did this project last winter and it took a lot of tinkering and quite a few hours. I’d do it again because I’m happy with the outcome, but it may not be for everyone.
First, messing with your engine cooling system poses some risks such as overheating/engine damage and voiding your warranty. Do this at your own risk. To get comfortable with these risks I went step by step and tested my work. With regard to warranty, I decided to not make any permanent modifications to the original equipment, just added some new parts and hoses to connect it all. I can re-install the original hoses and restore the system back to stock in just a few minutes. Draining and refilling the antifreeze takes a little longer.
There are probably many ways to do this type of project, this is just the way I choose. I used a 3 way valve on the heater core supply line and plumbed in a brazed plate heat exchanger, so that I either have flow thru the heater core or thru the new heat exchanger. I used a ¾” valve because I couldn’t find any ½” full port 3 ways and I didn’t want to restrict the flow to the heater core. It’s important to use a valve with enough temperature rating, such as one rated for steam service. I used brass/bronze so I could solder copper fittings to the body (be sure to disassemble the valve and remove the seals before soldering). The exchanger I used was a 20 plate model from Duda Diesel with ½” mpt connections.
The biggest challenge was fitting everything into the cramped engine compartment. I eyeballed where I wanted the exchanger and valve so that all the hose connections would be possible, and then fabricated a bracket to mount the valve to the block using two existing alternator bolts. Initially I made a bracket from very thin gauge metal that was easy to bend and form, got it how I wanted it, then used it as a template to make a heavier (1/8” thick) bracket. Most of the hose connections were short with tight bends so I used copper sweat fittings and heater hose. To keep the valve and fittings as compact as possible, I used face bushings and street ells and fabricated my own hose barbs by rolling a ridge in short lengths of copper tubing.I mounted the heat exchanger to the frame at the top side of the coil spring housing with 3 nutserts. I used a little rubber between the mounting bracket and the exchanger. The last part was fabricating a valve handle that was easily accessible from the top of the engine compartment.
I’ve thought about installing a pressurized water system using the rear bumper for storage and tieing it into the heater, but for now I just pop the hood and set my 5 gal jug on top of the radiator and gravity feed thru the heater. I get about ½ gpm thru the exchanger this way and plenty of temp rise on the water … 80-100 deg f w/hot engine, and 40-50 deg f rise w/cold engine after 3-4 min.
The total cost for everything was ~$175 for me…. $33 Kitz ATK ¾” 3 way valve - EBAY, $73 Brazed plate HX - DUDADIESEL, $15 Nutserts & tool - PEGASUS AUTO, ~$50 in misc fittings, etc. I’ve got about 15,000 highway miles since installation and no problems. Heater (cab) still works great. Here’s some pics, questions or comments welcome.
FLOW DIRECTION
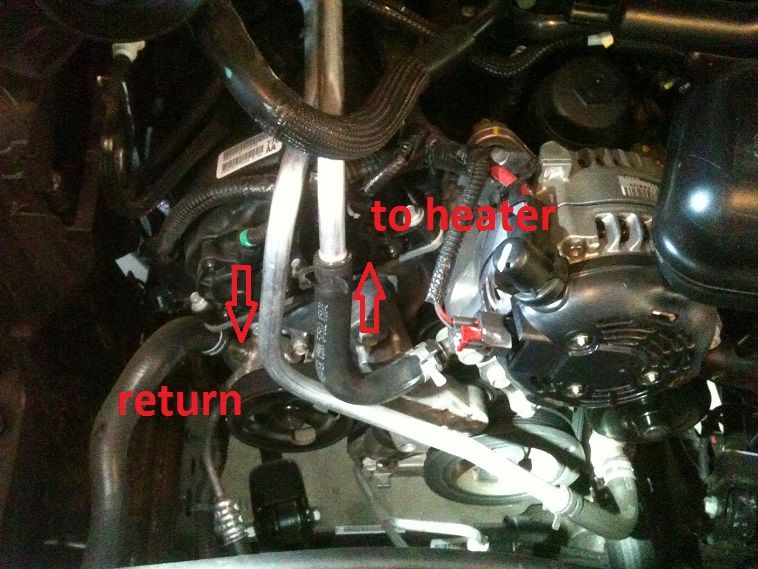
SCHEMATIC

BRAZED PLATE HEAT EXCHANGER

BRACKET FOR HEAT EXCHANGER

HX MOUNTING LOCATION UNDER AIR CLEAR & NUTSERTS

3 WAY VALVE & BRACKET

PRESSURE CHECKING VALVE & FITTINGS

VALVE MOUNTED TO BLOCK

RETURN LINES FROM HEATER CORE & NEW HX

COMPLETED INSTALLATION

3 GAL @ 120f IN 10 MIN
First, messing with your engine cooling system poses some risks such as overheating/engine damage and voiding your warranty. Do this at your own risk. To get comfortable with these risks I went step by step and tested my work. With regard to warranty, I decided to not make any permanent modifications to the original equipment, just added some new parts and hoses to connect it all. I can re-install the original hoses and restore the system back to stock in just a few minutes. Draining and refilling the antifreeze takes a little longer.
There are probably many ways to do this type of project, this is just the way I choose. I used a 3 way valve on the heater core supply line and plumbed in a brazed plate heat exchanger, so that I either have flow thru the heater core or thru the new heat exchanger. I used a ¾” valve because I couldn’t find any ½” full port 3 ways and I didn’t want to restrict the flow to the heater core. It’s important to use a valve with enough temperature rating, such as one rated for steam service. I used brass/bronze so I could solder copper fittings to the body (be sure to disassemble the valve and remove the seals before soldering). The exchanger I used was a 20 plate model from Duda Diesel with ½” mpt connections.
The biggest challenge was fitting everything into the cramped engine compartment. I eyeballed where I wanted the exchanger and valve so that all the hose connections would be possible, and then fabricated a bracket to mount the valve to the block using two existing alternator bolts. Initially I made a bracket from very thin gauge metal that was easy to bend and form, got it how I wanted it, then used it as a template to make a heavier (1/8” thick) bracket. Most of the hose connections were short with tight bends so I used copper sweat fittings and heater hose. To keep the valve and fittings as compact as possible, I used face bushings and street ells and fabricated my own hose barbs by rolling a ridge in short lengths of copper tubing.I mounted the heat exchanger to the frame at the top side of the coil spring housing with 3 nutserts. I used a little rubber between the mounting bracket and the exchanger. The last part was fabricating a valve handle that was easily accessible from the top of the engine compartment.
I’ve thought about installing a pressurized water system using the rear bumper for storage and tieing it into the heater, but for now I just pop the hood and set my 5 gal jug on top of the radiator and gravity feed thru the heater. I get about ½ gpm thru the exchanger this way and plenty of temp rise on the water … 80-100 deg f w/hot engine, and 40-50 deg f rise w/cold engine after 3-4 min.
The total cost for everything was ~$175 for me…. $33 Kitz ATK ¾” 3 way valve - EBAY, $73 Brazed plate HX - DUDADIESEL, $15 Nutserts & tool - PEGASUS AUTO, ~$50 in misc fittings, etc. I’ve got about 15,000 highway miles since installation and no problems. Heater (cab) still works great. Here’s some pics, questions or comments welcome.
FLOW DIRECTION
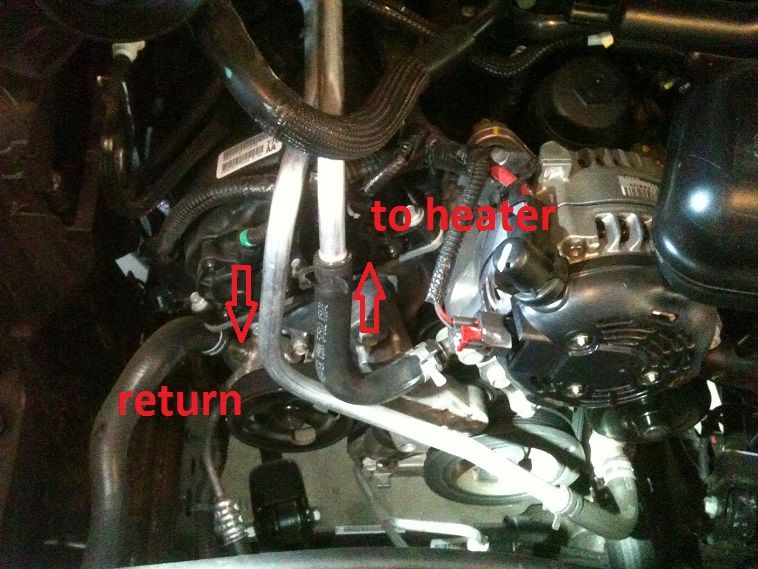
SCHEMATIC

BRAZED PLATE HEAT EXCHANGER

BRACKET FOR HEAT EXCHANGER

HX MOUNTING LOCATION UNDER AIR CLEAR & NUTSERTS

3 WAY VALVE & BRACKET

PRESSURE CHECKING VALVE & FITTINGS

VALVE MOUNTED TO BLOCK

RETURN LINES FROM HEATER CORE & NEW HX

COMPLETED INSTALLATION

3 GAL @ 120f IN 10 MIN

#2

Looks like a pretty
idea
Which heat exchanger (size/model/# of plates) did you use? I'm planning on improving the camping abilities and this would fit the bill nicely
What tool did you use to roll the lip on the copper pipe for barbs?



What tool did you use to roll the lip on the copper pipe for barbs?
Last edited by 69mach1; 10-12-2013 at 08:19 AM.
#3

A small pump could be added in line with the heat exchanger and in parallel to the engine cooling so it won't be interrupted -- what was your consideration to avoid a pump?
Did you consider an electric water heater, and if yes, what was your rational for preferring a water heat exchanger?
Did you consider an electric water heater, and if yes, what was your rational for preferring a water heat exchanger?
Last edited by GJeep; 10-12-2013 at 12:47 PM.
#4

and I made a simple flaring tool using a 1/2 in bolt and 5/16 ball bearing. Drill and tap a hole down the center of the bolt and drill one in from the side for the bearing. Slowly tighten the screw to get the bearing to raise up while rotating the pipe to get it to flare. It worked ok for me, took a minute or two per fitting.
#5

A small pump could be added in line with the heat exchanger and in parallel to the engine cooling so it won't be interrupted -- what was your consideration to avoid a pump?
Did you consider an electric water heater, and if yes, what was your rational for preferring a water heat exchanger?
Did you consider an electric water heater, and if yes, what was your rational for preferring a water heat exchanger?
An electric heater would certainly simplify plumbing issues but I don't think you can get enough heat input or power to make it practical. Just penciling thru the numbers, to raise 1/2 gpm of water 50 deg f takes ~200 btu/min or ~3600 watts. I'm not very knowlegable about electrical things but I don't think you can get there with the 12v battery/alternator.
Thanks for your response on the other thread I accidentally posted. Made me mad, I spent quite a bit of time putting this write up together and still screwed it up. I did eliminate my original post, maybe a moderator will delete the whole thread.